微型双螺杆挤出机虽“小”,却在高分子复合材料研发中扮演着“关键角色”。通过合理设计螺杆构型、优化工艺参数,并结合创新配方,可以高效制备高性能、多功能复合材料。未来,随着智能化与绿色制造需求的增长,微型双螺杆技术必将进一步推动材料科学的突破!
1.微型双螺杆挤出机的核心优势
相较于传统单螺杆挤出机或大型双螺杆设备,微型双螺杆挤出机(通常螺杆直径在10-24mm)在复合材料研发中具有优势:
-精准的温控与剪切力:适用于热敏性材料(如生物基高分子、导电聚合物)。
-灵活的模块化设计:可调整螺杆组合、长径比(L/D),适应不同配方需求。
-低物料消耗:适合实验室研发,减少昂贵原料的浪费。
-高效的分散与分布混合:纳米填料(如碳纳米管、石墨烯)的均匀分散更易实现。
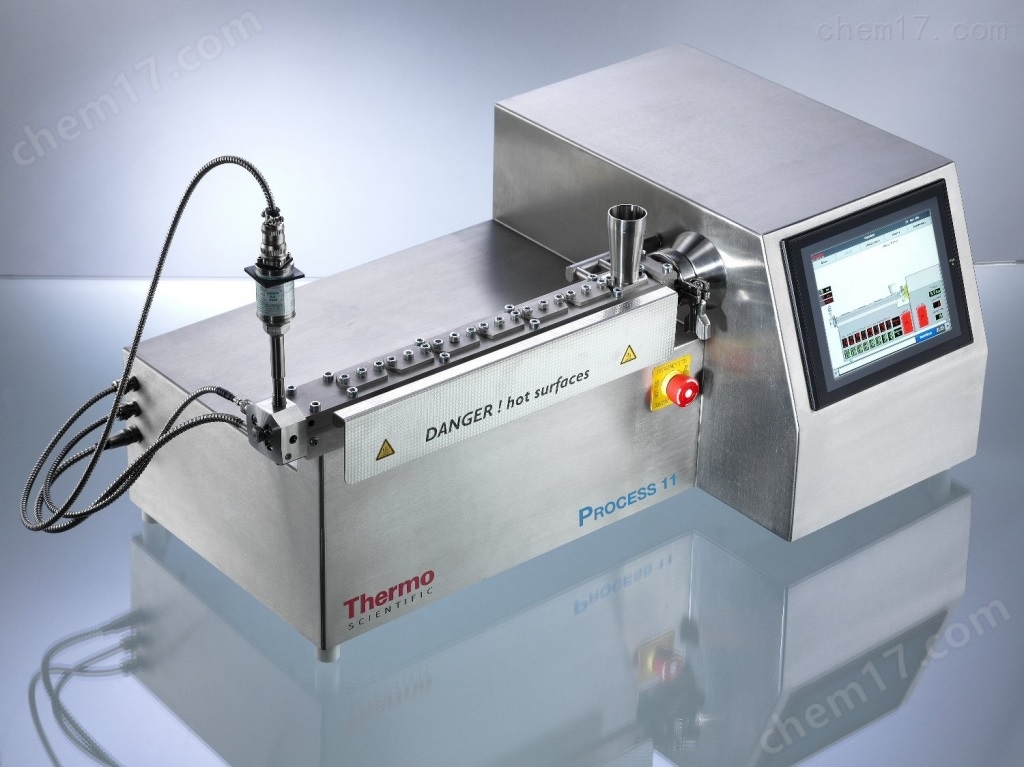
2.关键工艺优化策略
(1)螺杆构型设计:匹配材料特性
-剪切型元件(如捏合块):适用于高黏度体系(如PA/GF复合材料),增强纤维分散。
-输送型元件(如正向螺纹):保证物料稳定输送,避免过度剪切导致降解。
-反向螺纹+排气段:用于脱挥处理(如去除溶剂或小分子副产物)。
案例:制备PLA/碳纤维复合材料时,采用“高剪切捏合块+缓释输送段”组合,可避免纤维断裂,同时提升界面结合力。
(2)工艺参数优化
-温度分区控制:不同温区设置影响熔融与混合效果(如TPU基材料需低温塑化以防热降解)。
-转速与喂料速率:高转速(300-600rpm)可提升分散性,但需平衡停留时间以避免降解。
-真空脱气:用于去除气泡,提高复合材料致密性(尤其对光学级材料至关重要)。
(3)填料预处理与共混方式
-纳米填料预分散:如石墨烯先经溶剂剥离再与聚合物熔融共混,可避免团聚。
-多阶共混工艺:先制备母粒(如高浓度碳黑/PE母粒),再二次稀释,提升均匀性。
3.创新应用案例
(1)导电复合材料
-配方:TPU/CNTs(碳纳米管)体系,通过微型双螺杆优化剪切力,使CNTs形成导电网络,体积电阻率可降至10²Ω·cm。
-应用:柔性传感器、抗静电包装。
(2)生物可降解复合材料
-配方:PLA/PBAT/淀粉共混,通过螺杆组合调控相态结构,提升韧性和降解速率。
-应用:一次性医疗器械、环保包装。
(3)高强轻量化材料
-配方:PP/玻璃纤维(GF)体系,采用高长径比(L/D≥40)螺杆,使纤维长度保留率>80%。
-应用:汽车零部件、无人机结构件。
4.未来趋势:智能化与绿色化
-在线监测技术:结合红外光谱(NIR)或拉曼探头,实时分析复合材料成分均匀性。
-AI工艺优化:通过机器学习预测最佳螺杆组合和工艺窗口,减少试错成本。
-可持续材料开发:微型双螺杆适用于回收塑料升级再造(如rPET/天然纤维复合材料)。